Roadway and Asset Management System - RAMS
Roadway and Asset Management System - RAMS
The Roadway and Asset Management System’s (RAMS) development started in the late 1980s and has continued to evolve into the most comprehensive asset management system for use by public agencies. The system was developed with input from local public agencies and was developed to meet the needs specific to the work they do. Th system is customized to specific clients based on their requirements and manner of operation.
The system includes the following modules:
– Pavement Management System
– Maintenance Management System
– Sign Management System
– Bridge Management System
– Fleet Management System
– Asset Management System
Pavement Management System - PMS
The Pavement Management System (PMS) is the Module that allows Public Agencies manage their pavement infrastructure. It has provision to store and manage all the geometric and traffic features as well as performance information including condition and performance for all segment in the network. The system has utilities to generate new segments, merge existing segments into one larger segment or split an existing segment into smaller segments. The PMS is tightly integrated with the Maintenance Management System (MMS) described below.
We recently added a full financial modeling package using proprietary algorithms to create short and long term budgets with performance prediction and allow what if analysis.
Maintenance Management System - MMS
The Maintenance Management System (MMS) is used to keep track of all the work done on the road and street infrastructure.
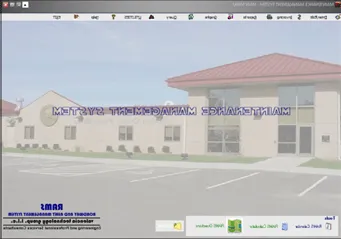
The system keeps track of all material, equipment and manpower used during M&R activities. The costs are assigned to individual segments.
The system generates work orders for all maintenance activities, both in house an contracted, and monitor the progress.
Materials – Maintains stockpile for materials owned and stocked by the agency. The cost of material is assigned based on quantity and used and current unit costs.
Equipment – Keeps track of all equipment used and derives the hourly costs from the Fleet Management System (FMS). It also has the capabilities to use standard FEMA rates when generating reports for reimbursement by FEMA.
Manpower – Uses the actual hourly rates for worker involved in the project including regular, overtime and double time rates.
The system keeps track of expenditures by assigning cost to specific Budgets and Line-Item numbers and notifies when budgets are running out of money, or the budget has been exceeded.
In conjunction with PMS, it can generate the full GASB compliant report.
Numerous reports including graphing of Maintenance cost and employee utilization.
The system has the same consistent look and operation is consistent across the various modules. The various modules interface seamlessly and without user intervention.
Sign Management System - SMS
The Sign Management System (SMS) is used to keep track of all the work done on the sign in the system. The system work in conjunction with the PPMS and MMS and every sign is assigned to a specific PMS segment.
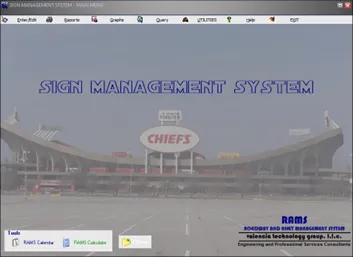
The system keeps track of all material, equipment and manpower used during sign M&R activities. The costs are assigned to individual segments.
The system maintains an inventory of signs as well as inspection data and all cost to maintain, repair or replace signs.
The system allows the creation of yearly program budget and line items to keep track of money spent. For example, the Sign budget can have Line Items such as repair, brush cleaning, post replacement, face replacement and so on. The system will notify when the expenses to date are getting close to the budgeted amount for the Line-Item budget to allow for proper budgeting.
The system has the capability of reading RFID tags during inspection and can also read data from Retro-Reflectometers for analysis and historical inventory of all data.
There are a number of reports available as well as capabilities to export data in many formats for use by other applications.
Bridge and Culvert Management System - BMS
The system includes a Bridge and Culvert Management System; however, many users choose to use the FHWA system. We can provide more details of this module upon request.
Asset Management System - AMS
This system was developed to provide a simple inventory of agency assets, such as office equipment and the operation is simple and consistent with the rest of the system.
Fleet Management System - FMS
The Fleet Management System (FMS) is used to keep track of all the work and activities related to the operation of a Fleet and its corresponding supporting infrastructure. The system was designed for use primarily by Public Works Agencies and it caters to the unique needs of these clients.
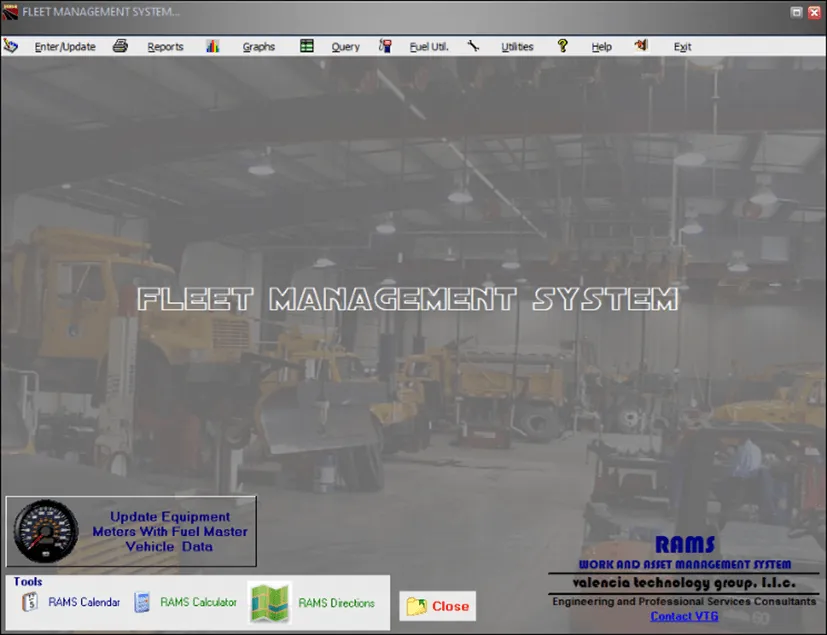
The system keeps track of all parts and labor used to maintain the fleet. It allows for multiple procedures per work order including Safety Inspections. It keeps track of parts inventories at multiple locations and allows transfer between locations. It also keeps track of vendors.
The system can keep track of equipment for multiple Departments within the Agency and prepare detailed intra-department billing using easy to follow procedures.
The FMS interfaces with Fuel Managements Systems such as Fuel Master and can get fuel and driving information in real time. The system downloads fuel and meter information at selected intervals for permanent storage.
The system has a very sophisticated and proprietary process to perform equipment evaluation using multiple user defined criteria. For example, the Finance Department can have one criteria based on present and future equipment value while the Operations side uses equipment serviceability.
The system has a massive number of reports and can answer any questions about any piece of equipment directly.
The system is completely stand alone and does not need any externa application to do its work.
Equipment – complete inventory of all equipment and properties. The Main equipment form allows accessing all information for any piece of equipment easily and quickly.
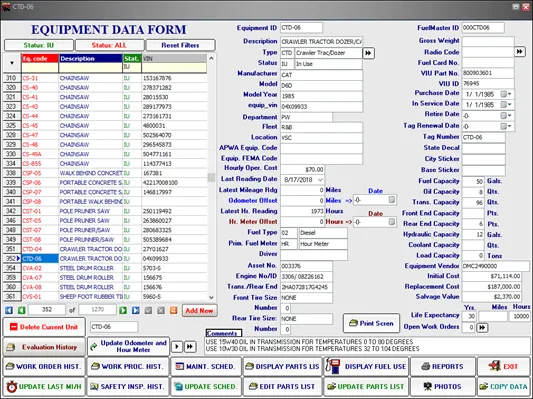
From this form we can access the entire Work order history…
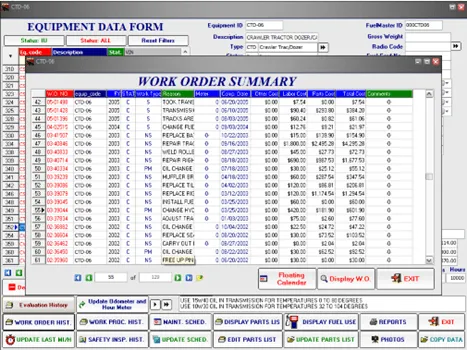
And the details of any specific Work Order, including summary and details…
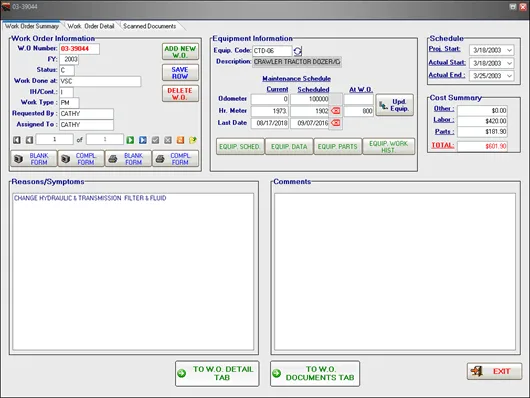
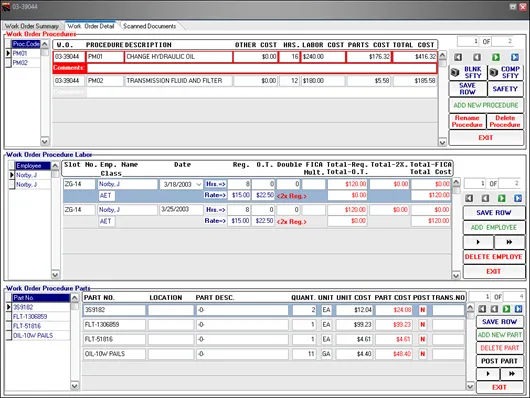
From the Main Menu we can access…

The maintenance Schedule for every procedure. The maintenance schedule can be set up by mileage, hours of calendar days…
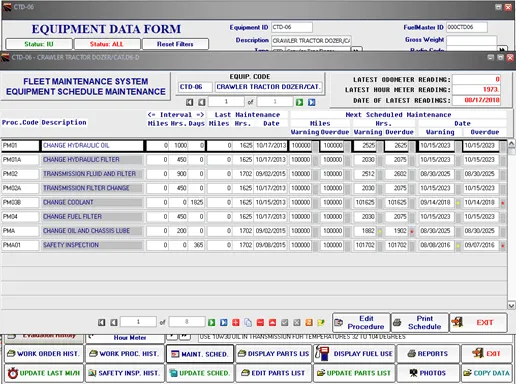
The parts for the equipment…
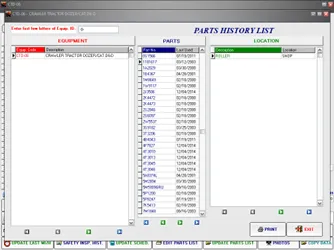
The fuel used for any time interval…

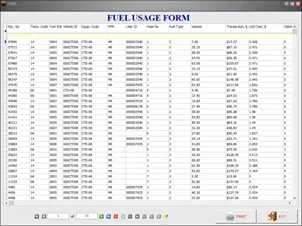
Safety Inspection History…
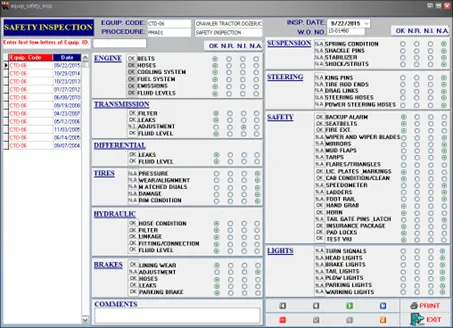
Photos for the equipment (can be marked up)…
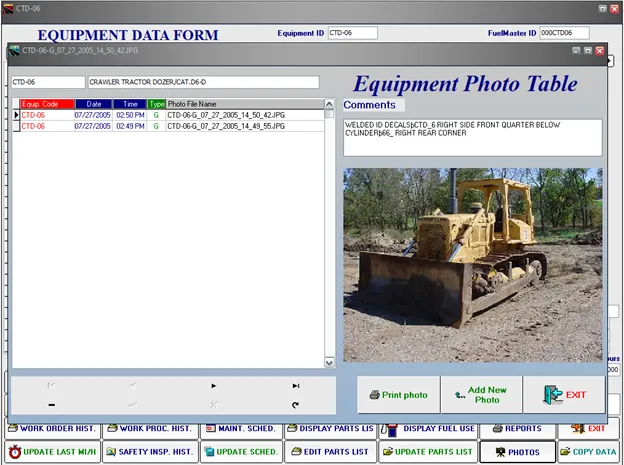
This just a very brief description of the system capabilities. You can contact us for very detailed demonstration and an evaluation copy of the entire application.